For those immersed in the world of oil extraction, the pressing screw of an oil press machine stands as a crucial component, often determining the efficiency, yield, and quality of the final product. This seemingly modest part requires a thorough understanding for anyone seeking to refine their craft or business in oil production.
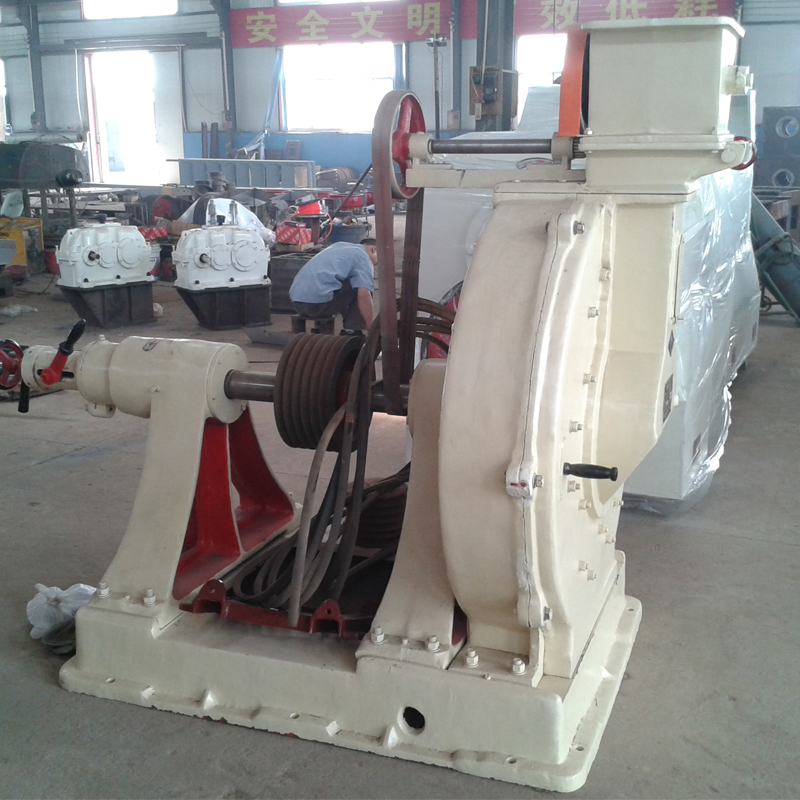
Pressing screws are designed with precision to manage the force and efficiency needed in separating oil from seeds or nuts. They function via a unique mechanical process that applies pressure to the raw material, extracting the oil while leaving behind the residual biomass, often referred to as cake. The efficacy of this process is highly contingent upon the design and material of the pressing screw itself.
Expertise in selecting the right pressing screw begins with an acknowledgment of the material to be processed. Different seeds or nuts possess varying hardness and oil content, requiring specific adjustments in screw design. For instance, seeds like sunflower or canola necessitate a different approach compared to harder nuts such as almonds. The screw’s design, including its diameter, pitch, and the number of flights, must align with the material characteristics to optimize extraction efficiency and minimize wear.
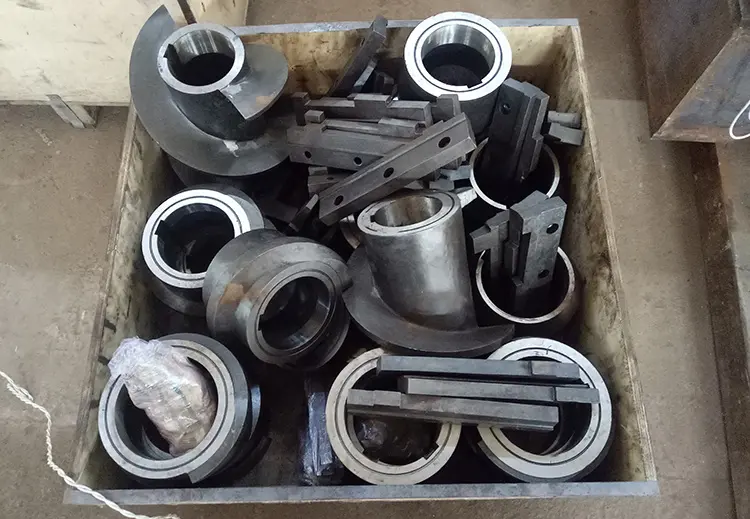
Material selection for pressing screws is another vital consideration. High-quality alloy steels or stainless steels are often preferred due to their durability and resistance to wear and corrosion. Given the intense pressure and potential chemical interactions involved in the oil extraction process, these materials prolong the lifespan of the screw and maintain the quality of the oil extracted. This choice reflects an understanding of the environment inside an oil press machine, where temperature, friction, and material hardness converge.
pressing screw of oil press machine
Authoritativeness in the field is sustained by favoring suppliers renowned for precision engineering. A credible source will not only supply superior pressing screws but also offer guidance tailored to specific needs. They also commit to quality testing, ensuring that each screw meets stringent industrial standards. An authoritative voice in the industry will discuss not only the specifications but also insights into maintenance and the role these screws play in the lifecycle of the machine.
Real-world experience further informs the practical adjustment or replacement of pressing screws. Operators often find that over time, wear and tear can lead to a decline in performance. Regular inspection and maintenance of the pressing screw is recommended to prevent unexpected breakdowns and ensure optimal functioning. Implementing a maintenance schedule based on usage intensity and material type extends the operational life of the machine while ensuring consistent production quality.
Trust in a brand or particular pressing screw model comes over time through consistent results. Machines that demonstrate reliable performance, backed by pressing screws from innovators who are respected in the oil extraction industry, elevate the credibility of the business. Trustworthiness also develops from transparent communications from manufacturers regarding warranty, material provenance, and performance guarantees.
To encapsulate, the pressing screw in an oil press machine isn't just a component; it is the heart of the operation, promising efficiency, quality, and profitability. Its selection and care require an approach that blends deep technical expertise with real-world wisdom, informed by sound industrial practices. This confluence of knowledge fosters a robust understanding of oil extraction dynamics, promising a business that thrives on quality and reliability.